Hrvatski ![]() |
Award-winning student works made under the mentorship of employees of the Chair for Metal Structures
Tihana Đukanović, Marcela Medić: ANALYSIS OF THE SCAFFOLD BASE JACK DETAIL FOR THE RECONSTRUCTION OF THE ZAGREB CATHEDRAL, Award-winning student work for the Rector's Award, AY. 2022-2023, mentors: Prof. Davor Skejić, PhD., Assoc. Prof Marko Bartolac, PhD., Faculty of Civil Engineering, University of Zagreb, 2023. (link)
Two major earthquakes that occurred in 2020 have significantly damaged the Zagreb Cathedral. In order to prevent the collapse and rebuild the towers of the Zagreb Cathedral, an urgent structural project for a load-bearing scaffold was made. A multidirectional modular lightweight tubular scaffold was chosen for this solution. Due to the extensive damage to the towers, it was not possible to anchor the scaffold to the full height of the towers, but only to the lower part, which was only slightly damaged. This resulted in a particularly unfavourable cantilever static system and relatively large loads on the scaffolding base. Due to the complexity of the scaffold concept and the geometry of the towers, numerous non-standard solutions had to be implemented. A non-standard solution was also applied to the details of supporting the scaffold on the steel platform, which begins around the base of the towers, at a height of about 37 m from the ground. As a result, a detail for supporting the steel structure of the scaffold was designed, geometrically adapted for safe and easy connection to the steel platform. The aim of research in this work is the analysis of the behaviour of applied non-standard (NS) scaffold base jack detail. For this purpose, a comparison was made with the standard (S) scaffold base jack detail that is not adaptable for connection to the steel platform. Three specimens of both groups of scaffold base jack details were subjected to bending tests in a laboratory. The test results, in the form of force-displacement diagrams, show visible differences in the behaviour of standard (S) and non-standard (NS) base jack details. Generally, non-standard base jack detail has higher stiffness, but is also less ductile compared to the standard solution. This behaviour is due to the fact that non-standard detail has a plate with greater thickness and additional stiffeners. In addition, numerical studies were performed in ABAQUS software package, and the numerical models were calibrated with the results of laboratory tests of NS and S details. Since the laboratory tests didn’t take into account the influence of the axial force that occurs during exploitation, a parametric numerical study was conducted. Analysis has shown that the applied non-standard base jack detail is reliable for supporting the 70-meter-high scaffolding around the towers of the Zagreb Cathedral, which are subjected to complex load combinations.
Dora Golubiček, Lovro Novinc, Elena Perković: INFLUENCE OF ADHESIVE TYPE ON THE BEHAVIOUR OF STRUCTURAL CONNECTIONS BETWEEN ALUMINIUM AND STEEL, Award-winning student work for the Rector's Award, AY. 2022-2023, mentors: Prof. Davor Skejić, PhD., Assoc. Prof. Ivan Duvnjak, PhD., Faculty of Civil Engineering, University of Zagreb, 2023. (link)
When steel is welded to aluminium, a problem arises with this type of joint because of the different physical and chemical properties of these two metals. Welding in this case significantly reduces mechanical properties of the connection and changes the heat-affected zone so much that direct welding of aluminium to steel is still an open and very complicated issue. Another, more suitable, but not yet fully researched way to join aluminium to steel is the use of adhesives. Adhesive bonding as the most suitable method, stands out from other connecting methods because of its many advantages. One of the most important advantages is uniform distribution of stresses, followed by ease of use, little to no influence on the mechanical properties of the material, and the ability to join a wide variety of materials. On the other hand, the disadvantages of adhesive connections are the accurate surface preparation and the low peel strength, which will be described in detail later in the experimental part. This study shows the original research on the application of adhesives in joining aluminium and steel structural members. The experimental and numerical investigations carried out concerned the influence of four different types of adhesives on the behaviour of bonded connections between aluminium angles and steel plates. The influence of the surface preparation was investigated as well as the layer thickness of the individual adhesive types. Conducted, very complex, numerical analyses accurately reproduce the experimental behaviour of bonded connections, especially in the first phase of behaviour and can serve as a good basis for the future calibration of numerical models. Such models will be able to simulate the full behaviour of adhesively bonded connections. They will also serve as a good optimisation tool for the geometry of the joints studied and for the choice of the most suitable type of adhesive. This will also serve as a guide for future research that will eventually lead to more frequent use of adhesives in aluminium structures.
Andrea Rajić: BEHAVIOUR OF LIGHTWEIGHT BUILT UP COLD-FORMED STEEL-CONCRETE COMPOSITE BEAM IN BENDING, Award-winning student work for the Rector's Award, AY. 2020-2021, mentor: Asst. Prof. Ivan Lukačević, PhD., Faculty of Civil Engineering, University of Zagreb, 2021. (link)
Cold-formed C sections are not common in construction practice as part of composite beams and there are still no standardized procedures for their design. However, the literature survey has shown their exceptionally good load-bearing behaviour and the possibility of easy construction. In this study, it was analytically shown how the bending of composite beams, composed of steel profiles of class 3 and class 4, can be calculated with the plastic resistance of steel cross-section and how the types of connection in built-up cold-formed beams and the degree of shear connection between steel and concrete cross-section governing its bending resistance. The bending resistance of the considered beams by applying numerical parametric analyses in software ABAQUS/CAE has been calculated. It is shown that the bending resistance of composite beams composed of C sections connected back-to-back by point-based fasteners at different distances is different from the bending resistance in the case when it is assumed that the profiles are completely connected. Therefore, it has been proved that there is a dependence of bending resistance on the number and arrangement of point-based fasteners between steel sections as well as in the case of the number and arrangement of point connections in the composite joint between steel and concrete. The presented results give the basis for the adjustment of the bending resistance design procedure of composite beams depending on the connection between cold-formed steel profiles and the degree of shear connection.
Mislav Pedišić, Anđelo Valčić: OPTIMIZATION OF BUILT-UP COLD-FORMED STRUCTURAL ELEMENTS IN BENDING, Award-winning student work for the Rector's Award, AY. 2018-2019, mentor: Asst. Prof. Ivan Lukačević, PhD., Faculty of Civil Engineering, University of Zagreb, 2019. (link)
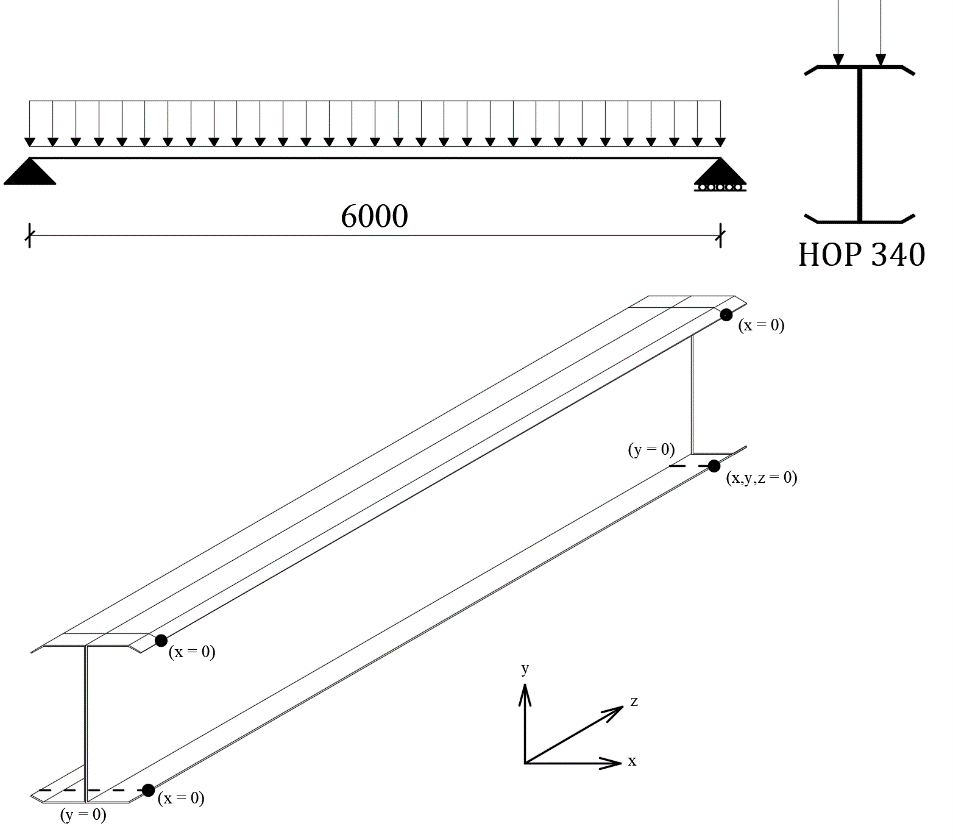
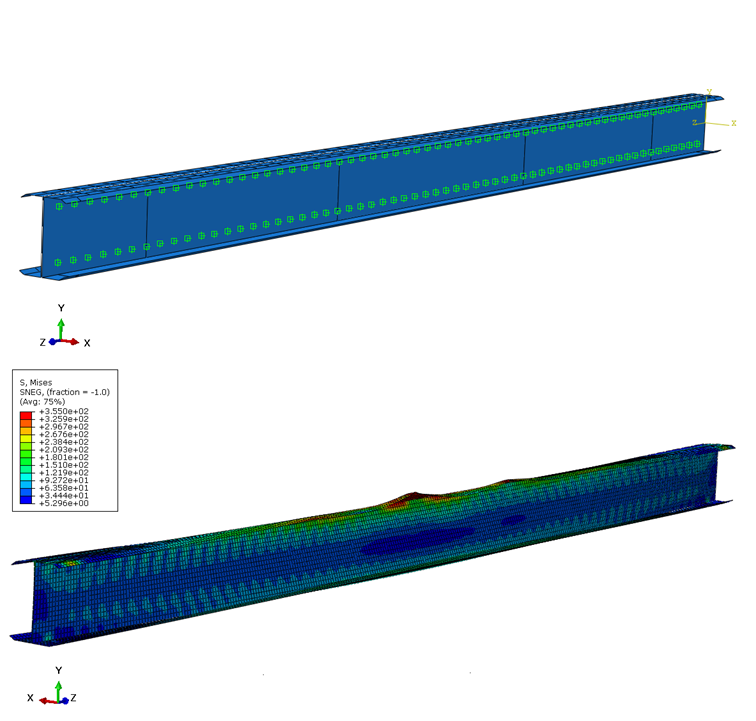
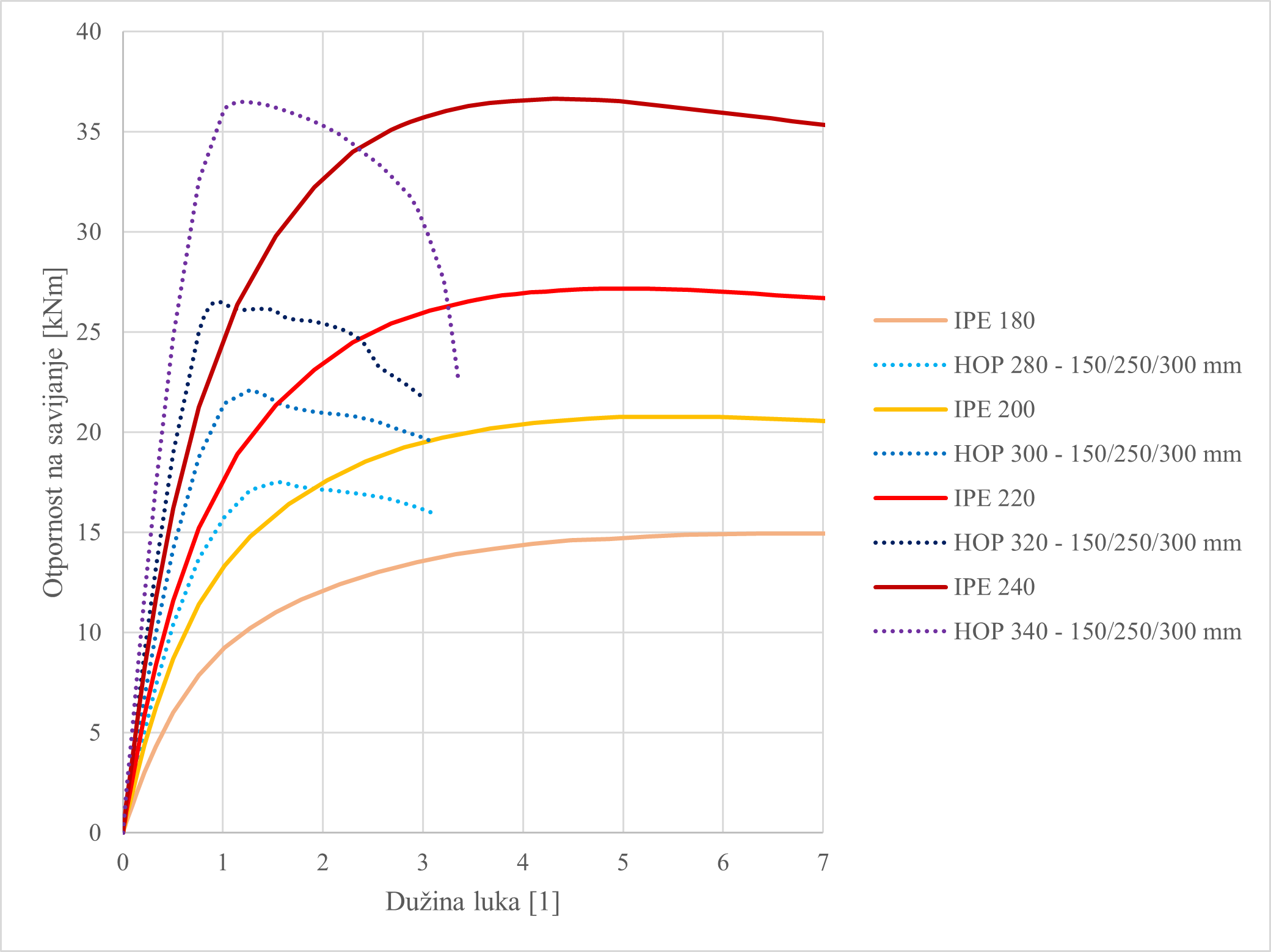
Built-up cold-formed structural elements can be very efficient structural elements, attractive due to material savings, but also for ease of construction. Therefore, built-up cold-formed elements are mainly used as load-bearing structural members or as various types of roof and wall sheetings. However, types of structural elements that still have the widest application in construction are hot-rolled elements. Taking into account the secondary elements in floor systems of multi-storey buildings or secondary beams in case of single-storey buildings, the most common application is narrow flange standardized European IPE section. Nevertheless, given a large number of such elements in structures, material savings using these elements, can significantly affect the reduction of construction costs. As a solution to this problem, this research deals with the application of cold-formed thin-walled elements as an alternative solution to secondary hot rolled IPE beams. The analytical and numerical parametric studies demonstrated in this paper has shown that with proper modelling of cross sections and with the favourable arrangement of connections, optimized built-up cold-formed thin-walled elements result in better characteristics than their counterparts (larger bending capacity), with lower material consumption and thus possibly lower construction costs. Based on the obtained results, further research in finding more favourable types of cross sections of cold-formed elements that can lead to even better alternative solutions is possible.
Anamarija Alagušić, Gabrijela Hrg, Marija Lokin: BEHAVIOUR CHARACTERIZATION OF THE STEEL GEODESIC DOME NODE, Award-winning student work for the Rector's Award, AY. 2016-2017, mentors: Assoc. Prof. Davor Skejić, PhD., Assoc. Prof. Domagoj Damjanović, PhD., Faculty of Civil Engineering, University of Zagreb, 2017. (link)
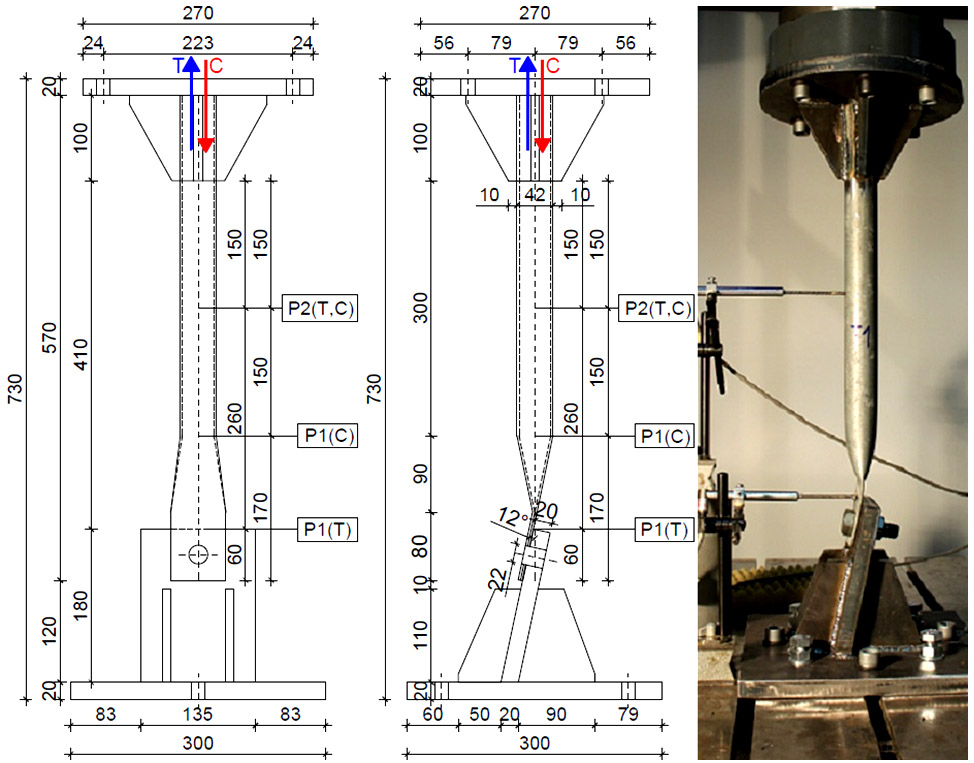
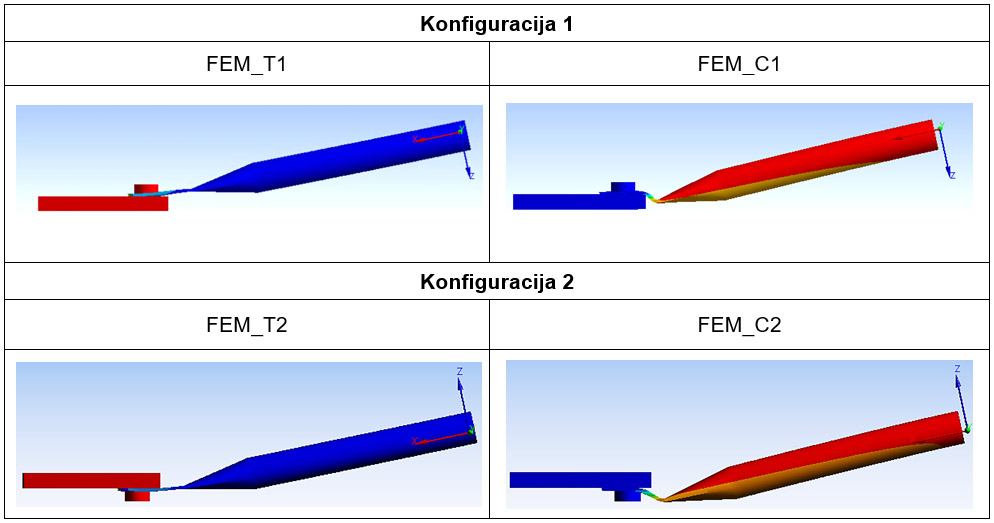
Geodesic domes are structures that nowadays, with their stability and aesthetics, are increasingly competing with other types of buildings that are more common in the world. Since the 1950’s their application has been found in cultural, housing and sports facilities. Throughout the years, various forms and techniques of mounting such dome types have been developed gradually together with nodal joints as important parts of the structure. The main subject of this research is the simplest solution of the dome node, which is optimal from the aspect of assembly. This node is formed as a lap connection composed of 5 to 6 truss members with flattened ends that are bent and interconnected by one bolt. The disadvantage of such a node design is the emergence of second-order effects near the connection due to the bending of the ends and the eccentricity of the force. As a consequence, the resistance of the connection, with respect to the resistance of the individual members, is significantly reduced. In order to improve the uniformity of the design of the dome structure, i.e. the assessment of the behaviour of such connecting mode the behaviour of one element in the node at the tensile and compressive loads was analysed in detail. Three approaches, i.e. research methods - analytical, experimental and numerical were implemented to determine the resistance of the connection. In practice, a simplified theoretical interaction expression is used to evaluate the critical cross-sectional resistance of the bended flattened tube part. Although it is most commonly used in practice, the disadvantage of this analytical approach is that the existence of eccentricity is taken into account regardless of internal force direction and the position of the element in the junction. Extremely unfavourable preliminary analytical results were the motivation for the extended experimental and numerical research. Experimental part of the research included testing of material properties of tubes and 6 specimens of tube connections. Three tube connections were tested in tension and 3 in compression. It was found that the failure of tensile specimens occurred due to the bearing around bolt hole and the failure of compressed specimens occurred due to the buckling of the flattened tube part. The force - displacement diagrams for two characteristic measuring points at the tube and force – stroke (testing machine) diagrams were obtained that describe the behaviour of samples under the tensile or compressive axial forces in the tube member. Analysis of the results revealed a great similarity in the behaviour of the samples. For the purpose of determining the actual properties of the material, a tensile test was performed on 6 standardized tubes extracted from tube samples. Numerical research was conducted using the ANSYS 15.0 software package. Based on the laboratory tests, 2 numerical models were calibrated depending on the load direction (tensile or compression). As only one geometric configuration in tension and compression was tested in the laboratory, the other configuration of the connection was analysed with two additional numerical models depending on the load direction. Based on the results obtained by numerical simulations, it was found that the buckling of the flattened part of the compressed element is relevant for the resistance of the node, for the second configuration of the connecting. After the extensive experimental and numerical research, behavioural characterization was performed based on the force - displacement diagrams. Among other things, the relevant resistance of the considered node connection was determined. Experimentally and numerically determined resistances showed a satisfactory correlation with respect to the analytical resistances calculated using the measured geometrical and mechanical properties. Based on the analyses carried out, a new solution for node design was proposed by connecting straight flattened tube end sections to a specially shaped steel plate. In this way, the adverse effects of eccentricity and second-order effects are annulled. In order to demonstrate the effectiveness of such a solution, additional numerical models have been made and based on the results of this analysis; the characterization of their behaviour was performed. Although numerical simulations have confirmed that the proposed design of the connection can remove the aforementioned drawbacks, this configuration has to be further researched. In order to obtain a more realistic behaviour of the node, it is recommended that the test should be conducted on a real node in one field or in a real dome. In the end, it should be emphasized that this is the first step in solving the practical engineering problem. The obtained results and the resulting conclusions are definitely in favour of fast assembly and uniform reliability of the entire structural system of geodesic domes. Conducted research is a contribution to safety of these structures which are used at various manifestations with large number of visitors.
Ivan Čudina: DETERMINATION OF THE ELASTIC CRITICAL MOMENT OF BEAMS WITH UNIAXIALLY SYMMETRIC CROSS SECTION BY USING NUMERICAL SIMULATIONS, Award-winning student work for the Rector's Award, AY. 2016-2017, mentor: Ivan Lukačević, PhD., Faculty of Civil Engineering, University of Zagreb, 2017. (link)
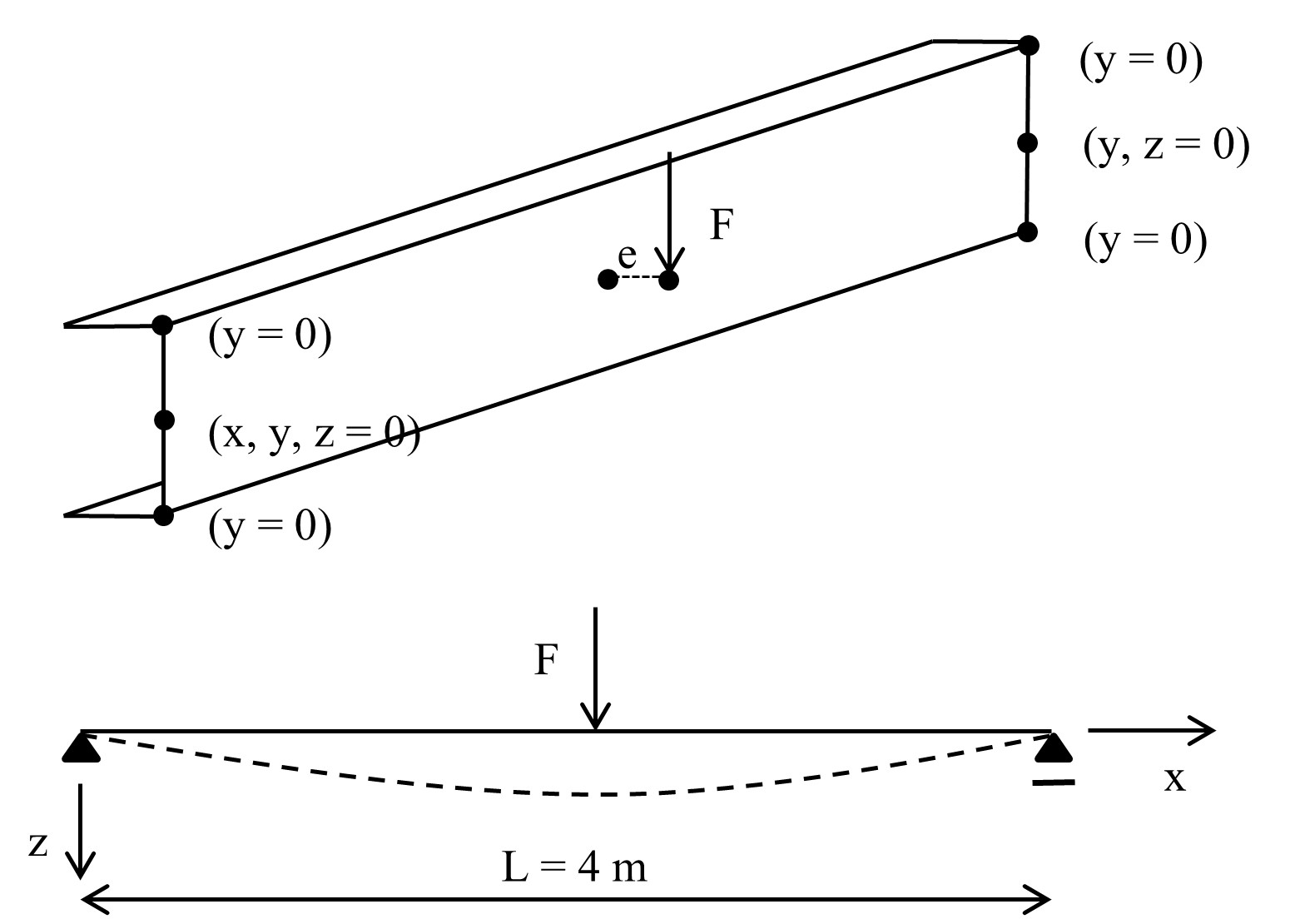
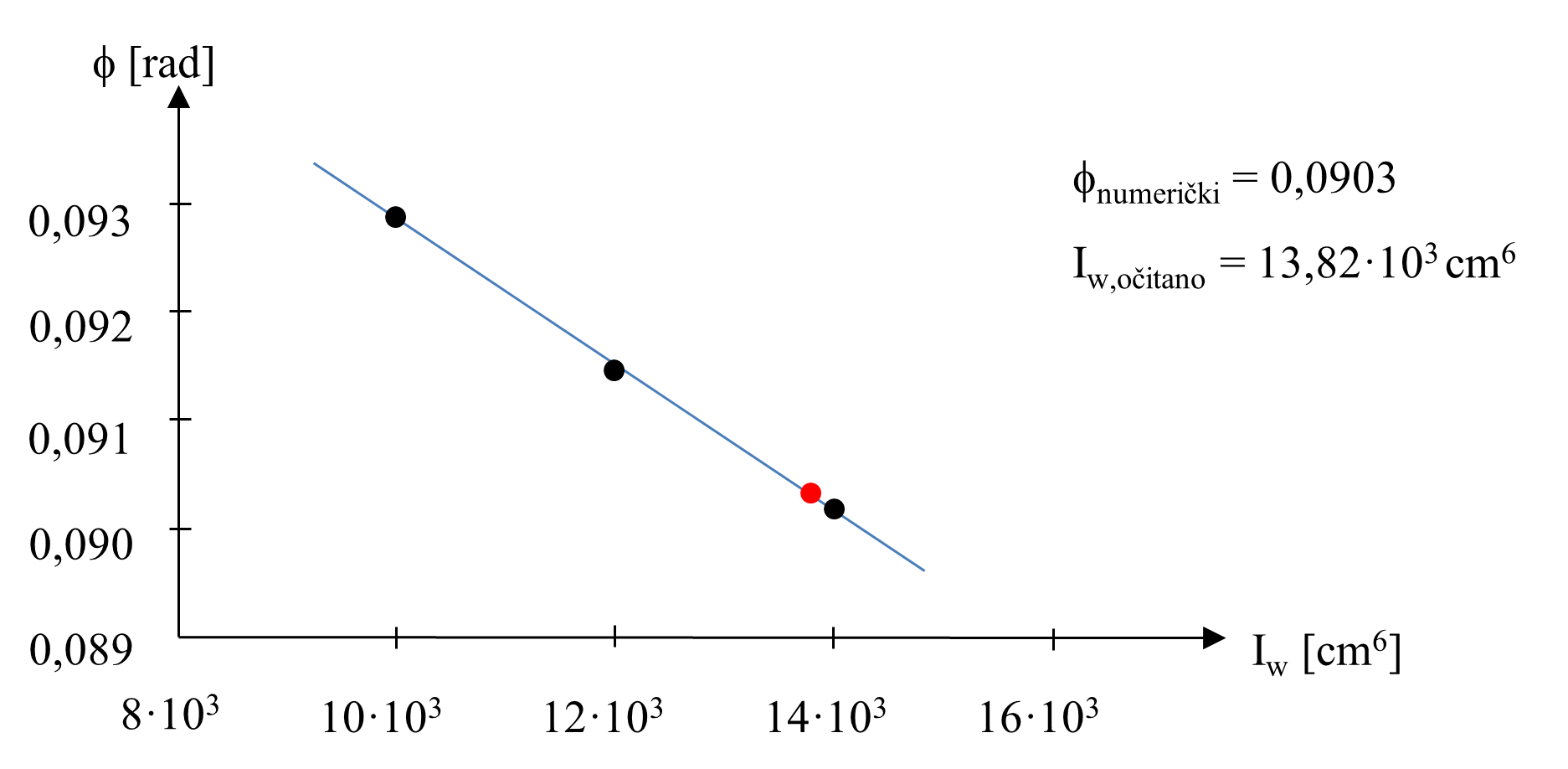
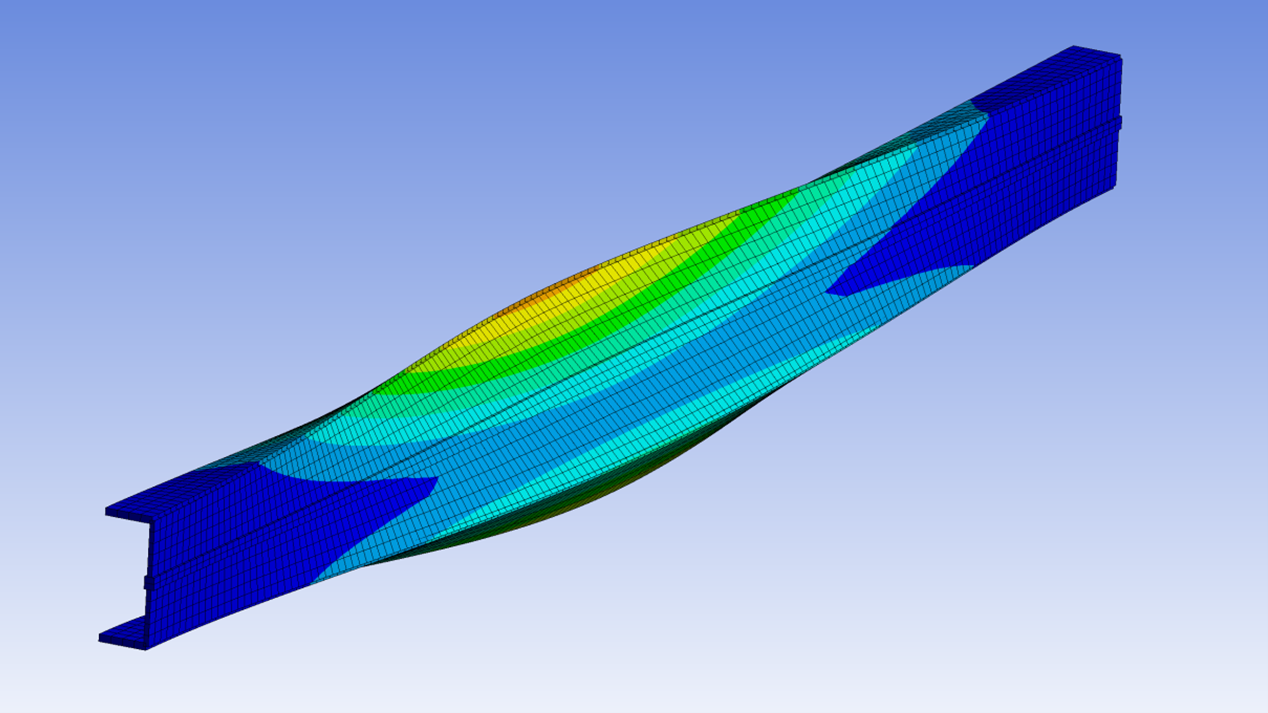
Hot rolled channel sections are frequently used as beams in structural engineering practice. However, in the European standard, or in any other standards in the world, there are no verification methods for lateral torsional buckling of channel sections. In available literature results regarding the determination of ultimate loads of channel sections are available, along with the proposed verification methods. However, the solution for calculation of the elastic critical moment of such beams is not provided. By conducting numerical parametric study using software package Ansys, elastic critical moment of beams made of channel cross section for different support conditions and different types of loading is calculated. It is shown that in certain cases some deviations of elastic critical moment for centrically and eccentrically loaded sections can occur, due to the effect of torsion that occurs during the eccentric loading. However, it was concluded that these deviations can be ignored provided that the channel section is subjected to web loading, which is almost always the case in structural engineering practice. Accordingly, it has been proved that the elastic critical moment of eccentrically loaded beams made of channel sections can be calculated in the same manner as in the case of centrically loaded beams with biaxially symmetrical cross sections. These results are a fundamental prerequisite for adjustment of the lateral torsional buckling verification method for biaxially symmetrical cross sections given in European standard to make its application possible for uniaxially symmetric cross sections.
Maja Milanović, Ivana Rogić, Ana Šitum: ASSESSMENT OF METHODS FOR CALCULATING STEEL BEAM FIRE RESISTANCE, Award-winning student work for the Rector's Award, AY. 2014-2015, mentor: Asst. Prof. Davor Skejić, PhD., Faculty of Civil Engineering, University of Zagreb, 2015. (link)
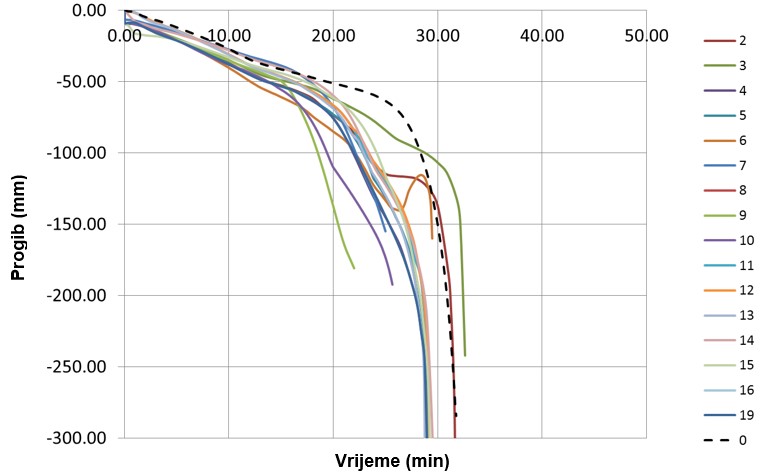
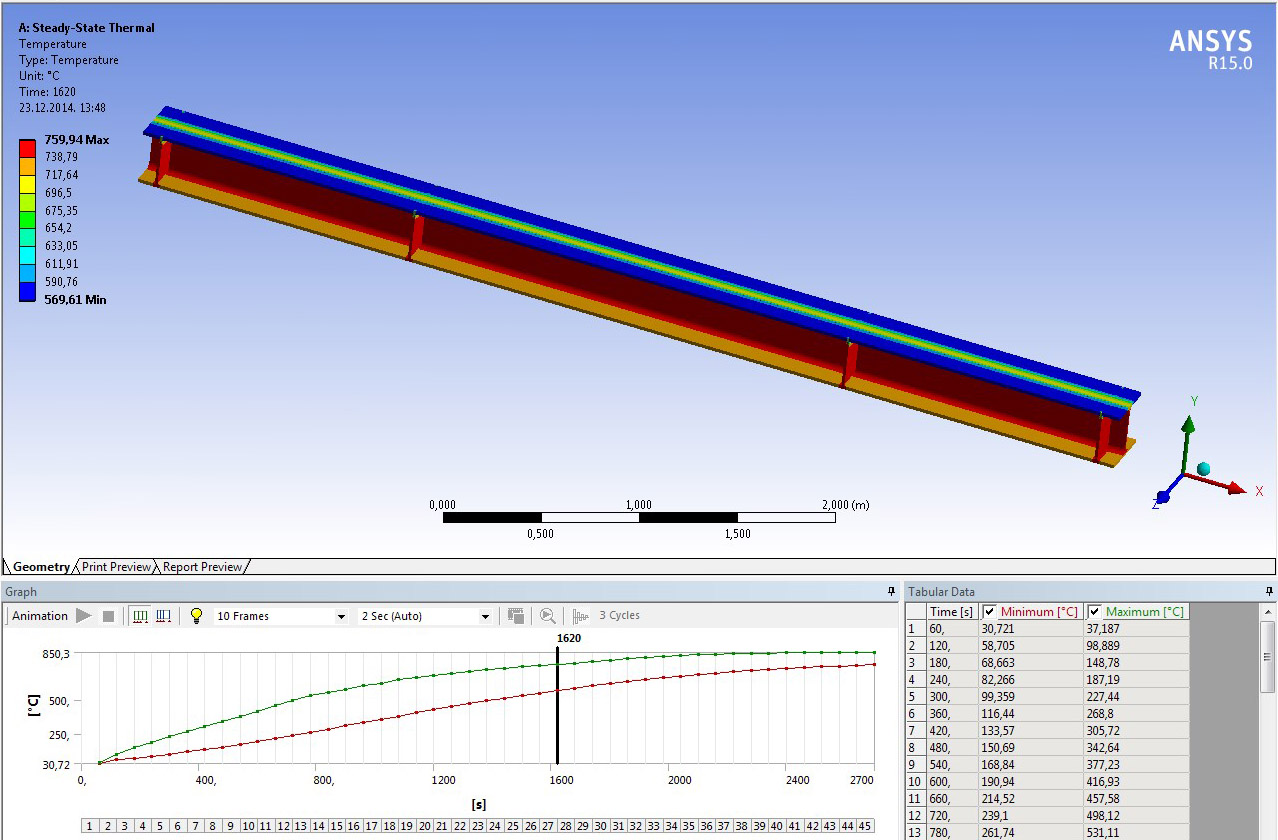
Fire engineering, as a relatively new scientific discipline, requires serious development in regard to the disastrous effects of fire on human life and property. This paper was written as part of the scientific research in order to improve resistance calculation methods for steel structural elements. According to previous experience, fire resistance assessment according to EN standards is mostly conservative. On the other hand, advanced methods are extremely unadjusted, which is understandable considering how many advanced softwares there are, and general knowledge and criteria equalization is unharmonized. In order to improve simplified standardized methods, they should be tested with laboratory results. It is much easier and cost-effective to improve simplified methods using numerical simulation that must be calibrated compared to test results. This paper describes first step and shows comparison between different method results and laboratory test results. It deals with simplified and advanced fire resistance calculation methods for steel beam. The use of simplified calculation form and software Elefir-EN is explained within standard methods. ANSYS is chosen as the sophisticated software for the advanced analysis. Furthermore, this paper presents international Round Robin study in which 11 participants, one of which was the Faculty of Civil Engineering, University of Zagreb, independently conducted fire resistance assessment analysis for steel beams based on equal input data. Beam with the same characteristics was subjected to laboratory testing in terms of the standard ISO fire in Technical Research Institute of Sweden, which initiated Round Robin study. Comparison of all study participants results, and a complete analysis given as University in Zagreb's (Faculty of Civil Engineering) contribution for the international research is shown. After the elaboration and discussion of the results, it has been concluded, contrary to expectations, that European standards overestimate fire resistance of this 'trivial' problem. On the other side, the advanced methods give extremely unadjusted assessments due to its complexity and uneven level of knowledge and failure criteria. It is recommended to expand further research with new laboratory tests which will result with rules for modelling with advanced methods and harmonized failure criteria. Only then, with calibrated numerical methods, the improvement of simplified calculation methods can be realized to assure required reliability level at the European level .